Choix des outils : HSS ou Carbure ?
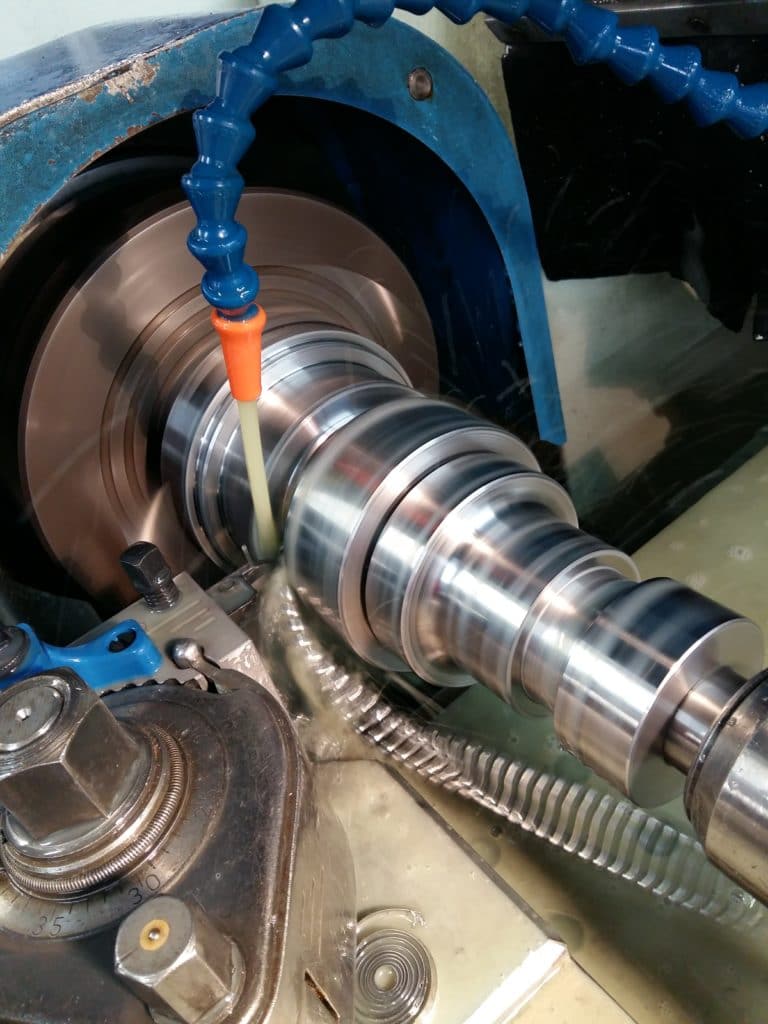
Vous venez d’acquérir votre nouvelle machine, tour ou fraiseuse, encore faut-il l’exploiter pleinement en utilisant les bons outils de coupe avec les bons paramètres !
Le type d’outil de coupe dépend directement de :
- Votre niveau de compétences
- Le type de machine : conventionnelle ou CNC
- Matière à usiner
- Travail à sec ou arrosage
Globalement, on a le choix entre le carbure de tungstène ou l’acier rapide supérieur (appelé généralement ARS ou HSS).
- Carbure de Tungstène
Le cas du carbure intervient particulièrement dès lors que l’on recherche des états de surface de haute qualité, une durabilité de l’outil (car en général on n’affûte pas les outils carbure ; il s’agit de plaquettes interchangeables dans le cas du tournage et de fraises monoblocs en fraisage) et pour l’usinage de matières dures (pré-traités). En revanche, la machine doit être adaptée car les vitesses de coupe sont 5 à 20 fois supérieures à celles utilisées pour l’usinage à l’ ARS, donc la plage de vitesse de rotation de la machine doit être suffisamment large !
De nos jours, le carbure est systématiquement utilisé dès lors que l’on travaille sur machine CNC car les paramètres de coupe affichés (vitesses d’avance, fréquence de rotation, profondeur de passe) sont précis et donc conformes aux recommandations des carburiers, ce qui permet d’optimiser au maximum la productivité.
Pour le cas du tournage (conventionnel et CNC), l’utilisation d’outils à plaquettes carbure interchangeables est un vrai confort de travail : plus d’affûtage, travail à sec possible, bonne durabilité de vie de l’arête de coupe, états de surface très corrects.
• Acier rapide supérieur (ARS)
En fraisage conventionnel au contraire, la pertinence de l’utilisation de fraises carbures n’est pas réellement démontrée dans la mesure ou il n’est pas conseillé de travailler en avalant (sauf machine équipée de vis à billes), alors que tous les carburiers préconisent le travail en avalant sauf cas spécifique.
Les outils HSS sont encore beaucoup utilisés en usinage conventionnel, notamment en fraisage car ils présentent le triple avantage :
- Du prix de revient
- De la possibilité de réaffûtage avec meule standard
- De la personnalisation de l’arête de coupe par affûtage en fonction de la matière à usiner
Mais la productivité est moindre eut égard aux faibles vitesses de coupe à utiliser et à la nécessité de réaffûter régulièrement ses outils, notamment lors de l’usinage de matières dures…
C’est la raison pour laquelle on trouve aujourd’hui beaucoup d’outils HSS dits « revêtus », c’est-à-dire traités après affûtage avec un revêtement améliorant considérablement la durée de vie : TIN, TiAln, TiCN etc… De plus, les outils HSS actuels sont généralement alliés de cobalt à des pourcentages variables allant de 3 à 10%, améliorant la dureté et la ténacité de l’ARS !
Gardons à l’esprit que pour l’usinage des matières tendres et/ou « collantes » : polyamides, plastiques techniques, aluminium AU4G, cuivre, laiton, les outils HSS actuels donnent de très bons résultats.